How to choose the best connection for your air or liquid cooling system.
A heat sink has to interact with both the power source and the cooling fluid. It is also required to connect to the industrial carpentry that will host the electronic device.
This article will help the reader to better understand the range of available connections, both for air and liquid cooling.
When selecting a forced convection solution, there are two main issues to consider:
- Cover: present or absent?
By choosing to use a cover, you have a functional, reliable surface for fixing the heat sink to the carpentry. In addition to this, the cover creates an artificial duct; the airflow goes through the heat sink without airflow bypass. If, however, you need a weight reduction or to save some costs, the cover can be avoided.
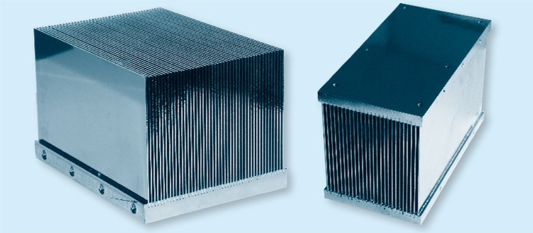
Heat sink without and with cover
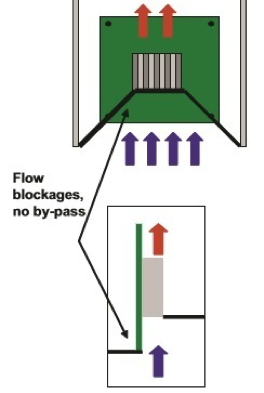
Ducted test method
- Fans: what’s the best mounting technique?
Deciding the best way to mount the fans is of paramount importance when setting up air-cooled devices. If you need a high performance heat sink, you could be forced to use a multiple fan solution. In this case size, overall dimensions and noise could be a problem.
The first issue (size) could be bypassed by mounting the fans directly in the heat sink:
The issue of overall dimensions is sensitive when, due to a miniaturization of the product, the fans must be moved away from the power source. Heat pipes can help, in this case, to shift the cooling system units.
Noise can be reduced using a thermal probe which triggers the fans just getting through a certain threshold.
A common and crucial theme for both heat sinks and liquid cold plates is convection: the dominant heat transfer mechanism in electronics. The convection heat transfer strongly depends on the fluid velocity and the area of the heat-transferring surface.
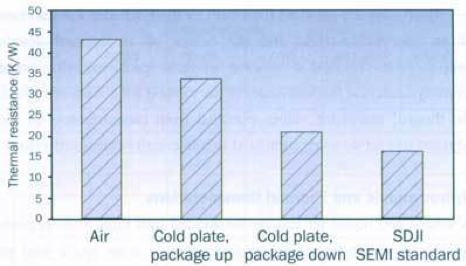
Air convection is usually the dominant heat transfer mechanism in electronics
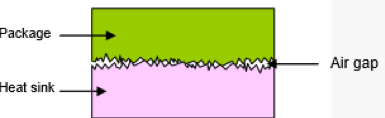
Air gap between a package case and a heat sink
When mounting a heat sink, it is normal to have an air gap between the package and the heat sink; this air gap is related to the surface roughness. Unfortunately, due to air’s insulative properties, the air gap significantly increases the thermal resistance. This can be reduced by:
- increasing the contact pressure
- introducing an interface material
Material Type |
Thickness (in) |
Thermal Resistance (°C in²/W) |
Mica/grease |
0.003 |
0.10 |
BN-Filled Silicone Sheet |
0.010 |
0.17 |
Kapton MT / Phase Change |
0.002 |
0.20 |
Kapton MT / BN-Filled Silicone |
0.006 |
0.25 |
Alumina-Filled Silicone Sheet |
0.010 |
0.45 |
List of conventional interface materials and their properties |
The following surface conditions are recommended for the heat sink:
- Flatness ≤16µm (reference length 0.8 mm)
- Surface finish ≤02 mm
Here are the most commonly-used heat source mounting techniques:
- Screw mounting is a traditional assembly method, involving the fastening of a screw, nut, and washer. Correct torque is the key factor in achieving adequate contact pressure between package and heat sink in order to minimize the thermal resistance.
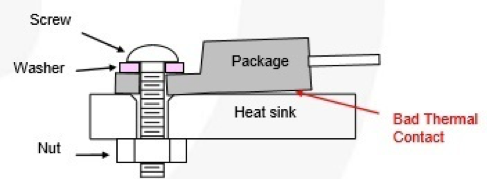
Bad assembly in screw mounting
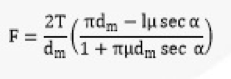
where l, dm, µ, and 2α are the pitch, mean diameter, friction coefficient, and thread angle (2α =60° for standard metric threads), respectively.
- Clip mounting has become popular because it is a simple and reliable mounting process, as well as being fast and appropriate for mass production assembly. The pressure on the package is uniform and thermally performing.
- Rivet mounting enables quick assembly in mass production, but it is difficult to disassemble and control the force applied to the rivet.
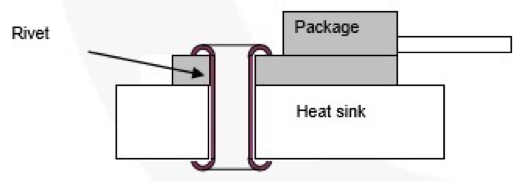
Example of rivet assembly
- A new technology, PowerSite™ allows packages to be soldered directly to the copper patch on the aluminum heat sink, which removes the problems of pressure dependency associated with mounting hardware and fasteners becoming loose. The copper patch improves thermal performance compared with manually applied thermal pads.
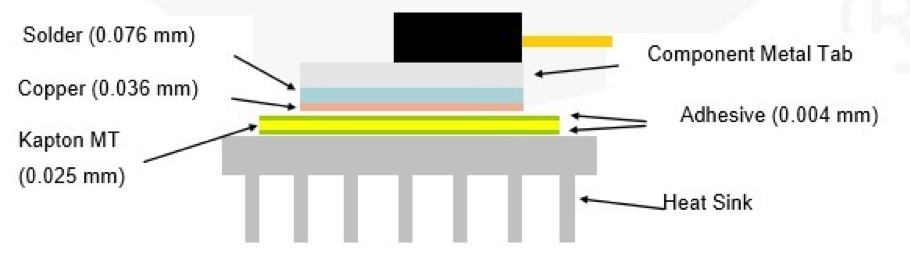
Package assembly with PowerSite™ Technology
- Pem® Soultions
PEM®S.E.T.™ stands for PEM® Surface Embedding Technology. These types of fasteners are pressed directly into the surface of the heat sink. This system has the advantage of eliminating operations for the attachment of mounting hardware; no drilling, tapping, or cleaning of the extrusion is required.
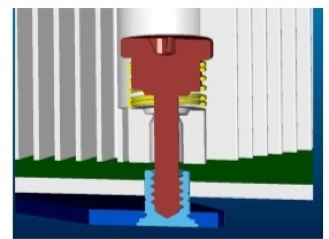
A section of one of the bolts
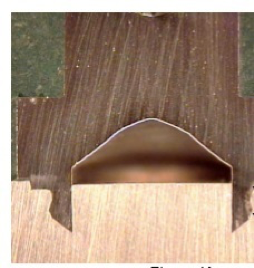
A cross section of the embedding portion of an installed part
When it comes to liquid cold plate devices, there is a multitude of choices in terms of fluid inlet and outlet:
- Connectors can be tailor made and brazed onto the LCP. This enables the user to overcome geometric issues related to commercial products: every size, slope, offset etc. can be achieved.
- When selecting commercial connectors, always avoid coupling copper components with an aluminum LCP; this will prevent otherwise unavoidable problems with galvanic corrosion.
- When using plastic or metallic connectors to mount a polymeric O-ring, it’s necessary to pay close attention to the use of thread lock or thread sealants, and read, in meticulous detail, the technical data-sheet. Most sealants aren’t plastic friendly!
Finally, we would like to mention some interesting couplings available on the market:
- Quick couplings: very useful for frequent installation and laboratory tests.
- Toggle clamp connections: used for quick fitting, without the need for threads.Sealing is guaranteed only by applied axial pressure and a gasket. Of crucial importance is the clamp centering, often assisted by neighboring centering holes.
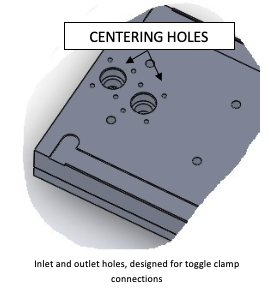
Inlet and outlet holes, designed for toggle clamp connections
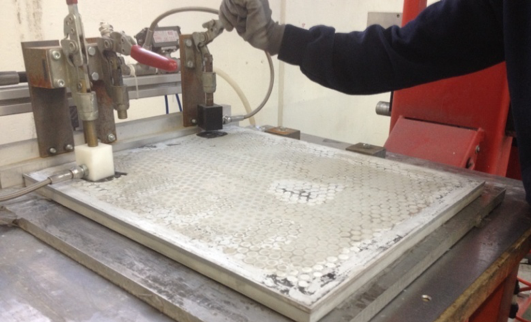
Aluminum LCP fast sealing test by Toggle clamp connections
- Hose connector: aminimal and cost-effective design, used in fluid application to connect FPT fittings (both brazeable and screwing).
- Custom designed products: for prototyping or R&D tests
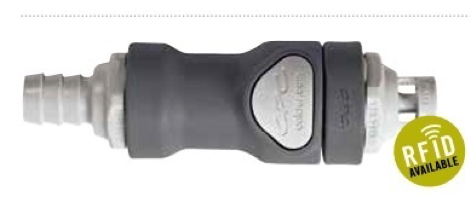
Non-spill coupling available with RFID (Radio-frequency identification)
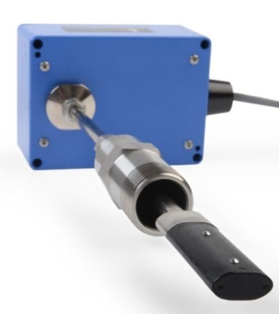
Insertion Magnetic Flow Meter
Connection is a huge world, but it doesn’t have to be a scary one. Demand the best technology for your thermal devices and … stay connected!
Click on the picture and download our free e-book
“Four Common Mistakes To Avoid When Selecting a Heat Sink”