Modern electronic devices, due to the increase of power density, require more and more efficient thermal systems to maintain their operating temperatures at a satisfactory level. On one side, the market imposes to reduce size and costs; on the other side, traditional materials are relatively heavy and don’t perform as well.
We will explore some alternative solutions in thermal management, including new materials which are increasing competitiveness in the market, leading to interesting opportunities for innovation.
First of all, it’s crucial to understand the role played by the material in the three ways to transfer heat:
1) CONDUCTION occurring through a solid or a stationary fluid. Materials have a direct influence on this heat transfer system. The materials are characterized by their thermal conductivity coefficient (k), expressed in W/mK, as per Fourier’s law
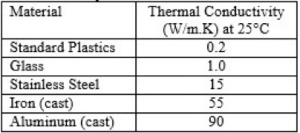
Conductivity values for standard material
2) CONVECTION from a surface to a moving fluid. A simplified approach can classify it according to the nature of the fluid (gas or liquid). The cooling effect of liquids is greater than that of gases.
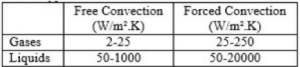
Typical convection coefficients
3) RADIATION between surfaces. This depends primarily on surface properties such as color, surface orientation, and temperature of the surface. Materials can play a secondary but still important role:
- final protection (Surtec)
- cleaning (sandblasting, washing and degreasing)
- preparation of the external surfaces (anodizing – black or colored, hard anodizing, etc.)
Common heat sinks are manufactured in metal, and particularly in aluminum alloys. Aluminum alloy 1050A, reaching 229 W/mK, has a high thermal conductivity value but it is mechanically soft. Aluminum alloys 6060 and 6063, with thermal conductivity values of 166 and 201 W/mK respectively, are commonly used.Both these alloys are suited for CAB brazing andCNC machining. Aluminum alloys are also lightweight, corrosion-resistant and cost effective. Copperhas approximately twice the conductivity of aluminum, but it is three times denser and four to six times more expensive, and it can’t be extruded. Copper heat sinks are machined and skived. Another method of manufacture is to solder the fins onto the heat sink aluminum nickel-plated base.
Alternatives to traditional heat sinks:
- Peltier Devices
In 1834, a scientist called Peltier discovered that if you take a thermocouple and apply a voltage, this causes a temperature difference between the junctions (later known as a thermo-electric cooler – TEC). As Peltier elements are active heat pumps, they can be used to cool components below ambient temperature. Heat transfer effectiveness through Peltier devices is increasable by using a heat pipe-based heat sink.
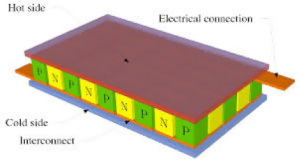
Peltier element schematic. Thermoelectric legs are thermally in parallel and electrically in series.
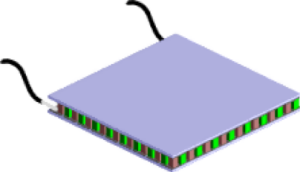
General diagram of a Peltier effect cell
- Heat pipes
Heat pipesusually have a metallic casing structure of copper or aluminum and present relatively high physical rigidity. Where the heat sink may be out of plane with the heat source (thus allowing heat removal from oscillating heat sources), a heat pipe was fabricated on a flexible liquid crystal polymer substrate using micro-machining techniques compatible with printed circuit board technologies. This device transfers up to 12W of power with an effective thermal conductivity of up to 830 W/mK.
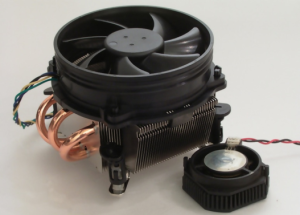
Hybrid design with a conventional fan arrangement, copper base, three heat pipes and aluminum fins
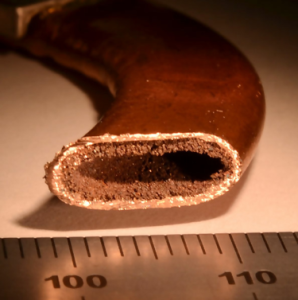
Cross section of a heat pipe
- Nanomaterials
Exchange materials made from nanomaterial-filled polymers are being designed for effective heat conductivity (more conductivity per unit area means less area for the same conduction) and cost reduction compared to conventional metals. Scientists developed and selected a number of polymer materials and nanofillers, including carbon nanotubes (CNTs) and metal-coated nanoparticles(NPs).
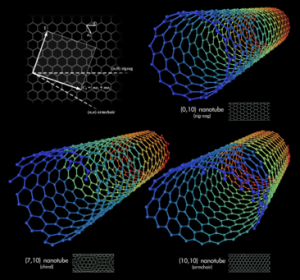
The (n,m) nanotube naming scheme can be thought of as a vector (Ch) in an infinite graphene sheet that describes how to ‘roll up’ the graphene sheet to make the nanotube. T denotes the tube axis, and a1 and a2 are the unit vectors of graphene in real space.
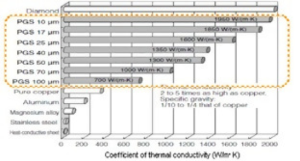
Comparison of thermal conductivity [a,b plane]
In recent years, nanomaterials have also been used in liquid cooling applications. In this case they are usually called nanofluids: suspensions of nanoparticles in base-fluids like water, ethylene glycol, oil and other cooling liquids.
According to preliminary research, nanofluids seem able to increase the convection coefficient of coolants by up to 30%.
- Replacement of traditional aluminum
- Thermally conductive plastics have the following benefits:
- Equivalent heat transfer/dissipation to aluminum
- 50% lighter than aluminum
- 3-dimensional complexity
- No antenna effect
- Simplified attachment
- Low cost
- Thermally conductive plastics have the following benefits:
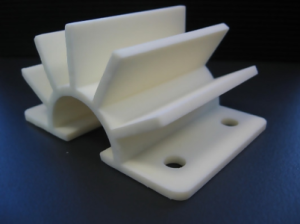
Polymeric heat sink sample
- Composite materials
Graphite is a material that’s gaining popularity with heat sink producers. But the real advantage of graphite is its weight: just 70% of the weight of aluminum.
Recently, Priatherm has developed an innovative air forced heat sink, where a base of aluminum graphite composite (a metal matrix composite based on graphite and aluminum, produced by pressure) is connected with a series of fins.
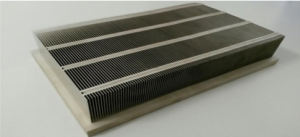
Aluminum graphite composite heat sink
- Ceramics
Ceramic combines two crucial characteristics: electrical isolation and thermal conductivity. It possesses good electromagnetic compatibility and has a thermal expansion coefficient close to semiconductor materials. Unlike other materials, its expansion coefficient and its thermal conductivity are the same in all directions. Ceramic is also waterproof, UV and corrosion resistant.
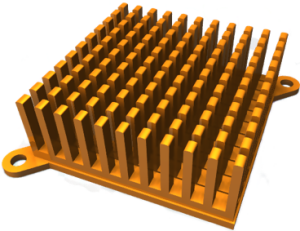
Ceramic heatsink
Click on the picture and download our free e-book
“Four Common Mistakes To Avoid When Selecting a Heat Sink”