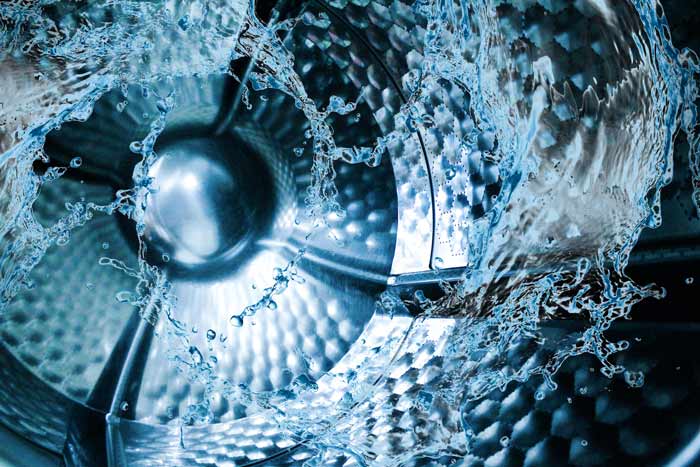
Introduction
Our daily life gets more and more simplified by smart systems in our houses and advanced technology domestic appliances.
Issues such as energy-saving, low polluting impact, flexibility in programming its use, require an electronic “brain” in our domestic appliances, which transforms our desires into machine commands.
Washing machines, both at the domestic level and, even more importantly, in the industrial sector, contain a PC Board with devices able to variate temperature, speed of the motor, quantity of detergent, cycle duration, etc.
The heat sink design and the metal container of the electronic part cannot be left to chance and requires the activity of co-design with thermal management experts.
Application field
Our customer is a worldwide leader in the manufacturing and sales of industrial and domestic appliances. They develop several projects and subassemblies in different countries around the globe, using local expertise and technology.
In the specific case of industrial washing machines, there are different teams, coordinated at a central level, that develop a new product from scratch to the final design.
- Mechanical engineers must study the metal structure and the engine, in cooperation with electrical engineers. Designers must create the external “envelop” to satisfy certain aesthetical criteria, but think about the interface between the machine and the user, who must find it easy and friendly.
- Electronic engineers develop the main PC Board, where many components in the circuit take control of the machine.
They ask thermal experts to co-design the heatsink that will remove the heat in excess from the core of the board to the outside. The heatsink must be cheap because the White Market has medium-high volume and big competition on prices.
A well-designed heatsink is not only used for cooling, it is used as mechanical support for the main box containing the electronic part, too.
The challenge
The difficulty of this project was related to mechanical more than thermal design. The customer needed a U-shaped extruded section, with:
- Fins on the sides to cool the heat
- Grooves in the open-top part and channels on the edges, to screw a metal cover
- Slots on the two lateral sides, to be able to place the PCB
- PT Click fins, to assembly TO220 components with stainless steel clips
The extruded heatsink, together with its main function of cooler, had to be developed in a way to create several supports to the mechanical assembly.
The challenge was to design the section wished by the customer respecting the feasibility rules for geometry (150 x 250 mm) and dimensional tolerances (± 1,25 mm), coming from the Extruders world.
A U-shaped extrusion, for example, tends to be deformed on top, making it difficult to respect a fixed distance between the two sides, where we wanted to insert the PCB without any risk.
Solution
The Priatherm team collected all the input data from the customer, asking several questions related to:
- the application
- the environmental
- the boundary conditions (the better the problem is known, the more accurate will the solution be)
After they selected the extrusion technology of aluminum alloy (EN AW 6060 T5) as the most suitable heatsink manufacturing process for this case, the engineers chose the best supplier for this extrusion tool.
It was evident that the main issue was to put all the mechanical requirements together in the same section, with complex geometry and demanding tolerances.
The co-design with experts of the extrusion process was key, to be added to Priatherm’s experience in cooling and the PT Click fixing system.
The idea to integrate fixing points for screws and PT Click fins for the clips’ assembly proved to be a smart solution to avoid further machining on the heatsink with an obvious save of manufacturing costs!
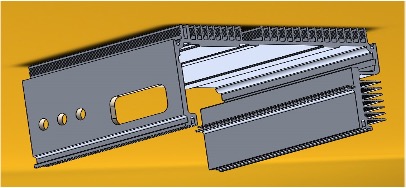
Top challenges
- Keep costs at the minimum
- Integrate several mounting features into the cooling solution
- Achieve and guarantee in time tight geometrical tolerances
Ask our Experts
Error: Contact form not found.